石英砂煅烧窑温度控制参数设定标准
石英砂煅烧窑是通过高温处理来去除石英砂中的杂质(如有机物、铁等),以提高其纯度,特别是在生产高纯度石英砂时。这一过程的关键在于温度的精确控制,因为温度过高或过低都可能影响煅烧效果和产品质量。以下是石英砂煅烧窑温度控制的一些基本设定标准和参数。
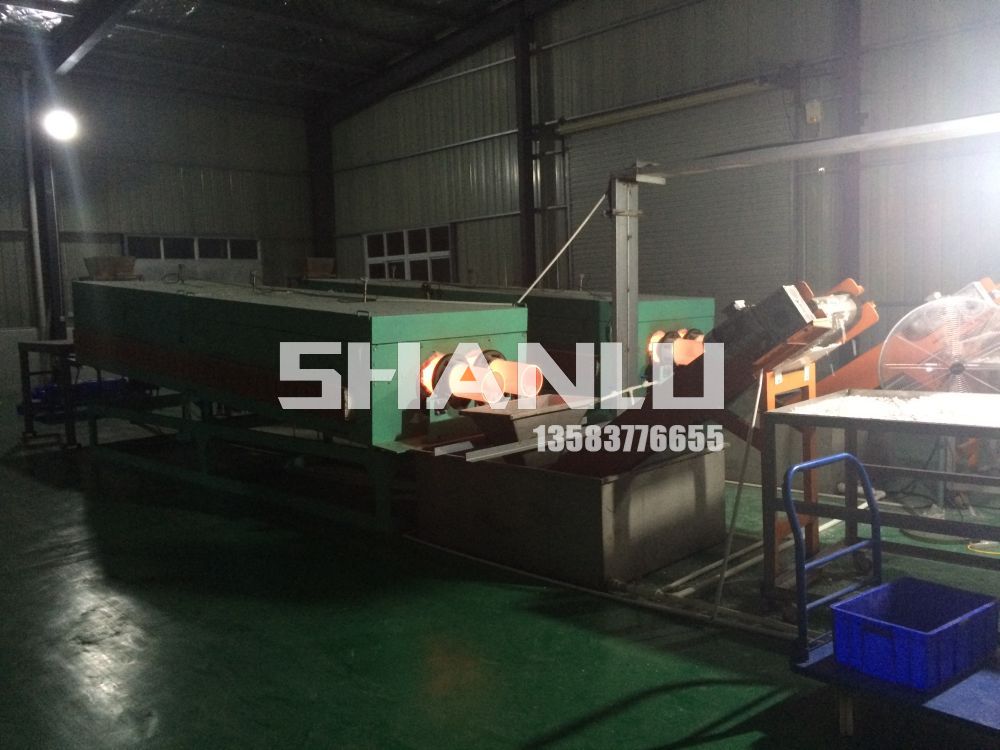
1. 煅烧温度范围
常规石英砂煅烧温度:一般情况下,石英砂的煅烧温度设定在 1000℃至1200℃
范围内。此温度范围足以去除有机杂质,同时不至于过度熔融或破坏石英砂的晶体结构。
高纯石英砂煅烧温度:对于高纯度石英砂的生产,通常需要更精细的控制,温度范围可设定在
1100℃至1300℃,以确保最大程度地去除铁、铝、钛等杂质,提升纯度。
矿物组成影响:石英砂中的杂质成分(如铁矿物、铝土矿、粘土等)会影响煅烧温度的设定。对于含有较多铁的石英砂,可能需要更高的温度来有效去除。
2. 温度控制参数
升温速率:升温速率对煅烧效果影响较大。如果升温过快,可能会导致石英砂的表面产生裂纹或过热,因此升温应缓慢。一般升温速率控制在 50℃/h 至 100℃/h
之间。
保温时间:煅烧过程中的保温时间取决于石英砂的粒度、杂质含量以及所需的煅烧效果。一般情况下,保温时间应保持在
2小时至5小时,以保证温度均匀分布,充分去除杂质。对于较大粒度的石英砂,可能需要更长的保温时间。
冷却速率:冷却速率也会影响石英砂的性质。快速冷却可能会导致石英砂中的晶体结构发生变化,影响其物理性质。因此,冷却速率通常应控制在 50℃/h 至
100℃/h,缓慢冷却能够确保石英砂的质量不受影响。
3. 温度分布与控制
窑内温度分布均匀性:煅烧过程中,窑内温度分布的均匀性非常重要。温度应保持稳定,避免局部过热或过冷。窑体内的温度均匀性可以通过合理的空气流动和热交换设计来保证。
温度传感器与自动化控制:为确保温度控制的精度,应使用高精度的温度传感器(如热电偶)和自动化温控系统进行实时监控和调节。温控系统应能够根据窑内不同区域的温度变化自动调整燃烧器的燃烧状态和风量。
多个温控区域:在一些大型煅烧窑中,可能会设置多个温控区段,每个区域独立控制温度。例如,窑前段可以使用较低的温度(约1000℃)进行预热,而窑后段则使用较高的温度进行主要煅烧。
4. 燃烧系统与气氛控制
燃烧气体选择:常用的燃烧气体包括天然气、煤气、液化石油气等。不同的燃料对温度的影响不同,控制气体流量和燃烧器位置非常重要,以确保窑内温度均匀。
氧气供应与气氛调节:石英砂煅烧过程中,需要控制窑内的氧气浓度,确保燃烧充分。窑内空气的供应量和气氛也需要调节,以避免形成还原气氛或过量氧化气氛,影响杂质去除效果。
5. 窑内温度监测与调整
实时温度监控:通过安装温度传感器并与自动控制系统相结合,能够实时监测窑内温度变化。常用的温度传感器有热电偶和红外温度传感器等。
温度自动调节:当温度波动超出设定范围时,自动化系统可以通过调整燃料供应或气流量来调整温度,保证窑内的温度稳定。
6. 质量控制与监测
样品分析:定期取样并分析石英砂的化学成分,确保其纯度和白度符合标准。如果石英砂的铁含量过高或白度不够,可以通过调整温度参数进行优化。
成品检验:煅烧后的石英砂需要经过粒度分析、纯度测试(如铁含量检测)和白度测试,以确保最终产品满足行业要求。
总结
石英砂煅烧窑的温度控制对于提升石英砂的纯度、白度以及最终产品质量至关重要。通过精确设定温度范围(1000℃至1300℃)、合理控制升温速率、保温时间和冷却速率,并确保窑内温度分布均匀,可以有效提高石英砂的煅烧效果。同时,采用自动化控制系统对温度进行实时监测和调节,是提高生产效率和产品一致性的关键。